Production Process
Quality products made of beech wood and other hardwoods.
1. Logging
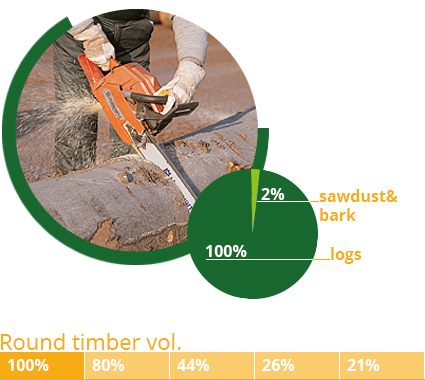
We are situated in an area surrounded by high quality forests wich provide supplies of almost exclusively PEFC-certified logs. Initially these are sawn into lengths, graded and segregated according to criteria of radius, length, quality, red heartwood, etc. This is important to ensure an optimal yield of timber for further processing.
2. Planking
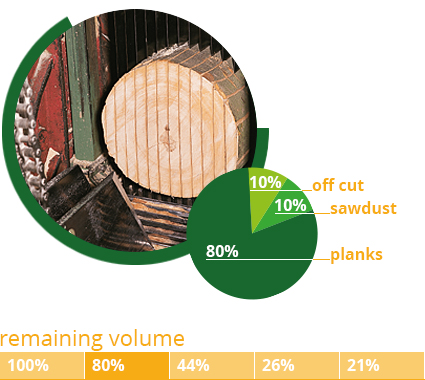
The logs are sawn into planks and graded according to quality, with the object of obtaining a quotient number of planks cut vertically to the grain. An 8-hour steaming process reduces the stresses caused during growth of the tree and also gives the timber a uniform colour, which later may be enhanced with a suitable veneer. The computer-controlled kiln drying process has a capacity of 32,000 cbm per year and provides an essentially improved product quality in comparison to drying in air.
3. Cutting
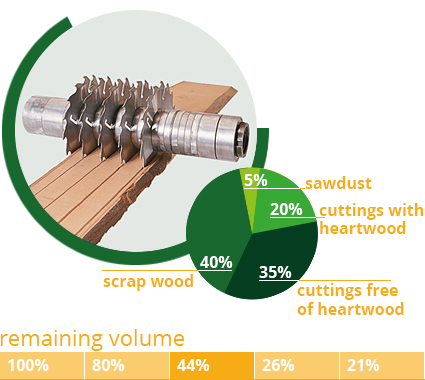
Cutting consists of 2 or 3 sawing processes:
1. To achieve maximum quality and optimum of timber yield, the planks are crosscut at suitably selected points.
2. These are edge trimmed and sawn with the grain into long strips.
3. Sub-standard quality and defects are marked, so that the computer may calculate optimum lengths of the best pieces according to our optimalised cutting lists.
4. Planing
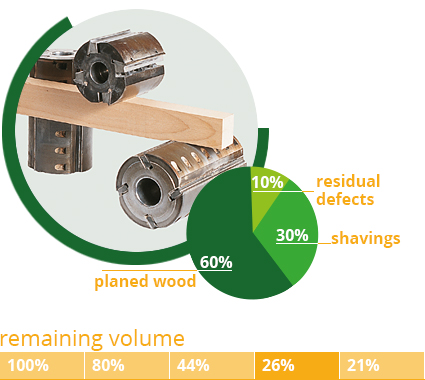
We utilise five automatic moulders providing a maximum of eight mandrills. The strips are accurately squared on four faces. By using modern machines a tolerance of a hundredth millimeter is achieved which provides the accuracy for the subsequent glueing process.
5. Boards
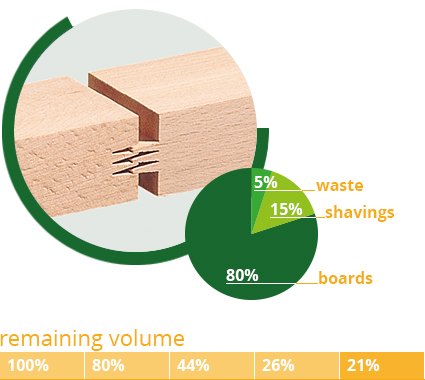
A finger jointing process adheres together the shorter lengths of timber into longer lengths, which are used for board production. This leads to a high utilization of timber which has the optimal stability.
A high frequency glue press heats the glued joint from the inside to the outside ensuring maximum strength and stability. The boards are trued to specified thickness by simultaneously sanding the top and buttom faces. Finally the boards up to 3.1 meters are cut into lengths, given a final inspection and shipped.